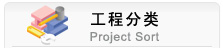
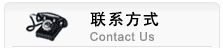
地址:镇江市学府路80号
邮编:212013
电话:0511-88791451
手机:13951280541
E-mail:jfchen@ujs.edu.cn
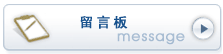

我国玻璃电熔的现状及今后的发展方向
由于环保的要求越来越高,玻璃制品的质量要求也越来越高,玻璃工厂采用电熔已经大势所趋。作者从事过十多年玻璃电熔化方面的技术研究和技术推广工作,参与设计、引进、翻版过数十座玻璃电熔窑、电加热料道、电辅助加热玻璃窑炉,帮助玻璃厂解决过多起玻璃电熔化和电加热方面的疑难问题。
进行玻璃的电熔化与电加热设计的单位和个人有数十家之多,设计的电熔窑各有特点,水平亦是参差不齐。在此作一总结。
1.玻璃的电加热料道
十年前,玻璃的电加热料道与煤气多喷嘴加热料道同时作为两项新技术在推广,有些厂家在考虑采用玻璃的电加热料道技术时,还要求到处考察。使用该技术的还仅仅是一些具有开拓精神的厂长。经过近十年来不断努力,玻璃的电加热料道已被广大的玻璃厂普遍接受,已成为了大众化的技术,有些单位和个人已把它制成了产品出售。
但一些特殊要求的和特种玻璃的电加热料道还是需要专业人员进行设计。玻璃的电加热料道大体分为硅碳棒辐射电加热料道、平板玻璃通路的电加热、板状钼电极的电加热料道、棒状钼电极电加热料道、混合式电加热料道、热套法电加热料道、料盆的电加热、氧化锡电极电加热料道等八类。
2.玻璃窑炉的电助熔加热技术
玻璃窑炉的电助熔加热技术主要用来:
(1)大幅度地提高熔化率。国外大型燃油平板玻璃池窑,一般熔化率为2T/m2·d,我国为1.6T/ m2·d左右,采用电助熔技术后,可使熔化率提高到3.2T/m2·d,甚至可达4.2T/m2·d。熔化率可提高60%,甚至100%。
(2)提高玻璃的熔化质量。在任何情况下采用电助熔都能改善玻璃的质量。这是因为加强了玻璃液的流动使玻璃液的均匀性提高了。在玻璃液中引入电能提高玻璃液的温度,从而玻璃液的粘度降低,澄清过程加快,熔解在玻璃液中的气体量显著减少,这对玻璃的成形和加工有良好的影响。
我国有些中小玻璃厂,由于燃料质量不好,熔化温度烧不上去,玻璃液质量很差。如果有条件采用电助熔技术,玻璃液质量将会得到很大的提高。
(3)灵活调节出料量。采用电助熔加热的池窑能够根据市场需要迅速调节池窑的出料量。在不增加池窑尺寸的情况下,池窑的熔化能力可提高30 50%。电助熔特别适合于需要定期变化出料量的窑炉。这种窑在使用期间熔制玻璃所消耗的矿物燃料不变,而电助熔可以使窑的熔化能力提高到最大限度。
(4)电助熔装置尤其适用于有色玻璃。如果是透热辐射性差的深色玻璃,则在熔化部使用电助熔极为有利。
(5)电助熔装置尤其适用于难熔玻璃。
玻璃窑炉电助熔加热的设计关键点是窑炉的电极排列和功率分布,对硼硅酸盐玻璃和有色玻璃的窑炉的电极排列是为了加强池底的能量,对为了增加产量或调节产量的玻璃窑炉电极排列是为了加强玻璃液的对流。
布置于池底的电极通电后,处于熔融状态的玻璃液为一导体。根据电阻的热效应原理,两电极间的玻璃液就会发热。同时,由于电极端部的边缘效应,电极端部附近的玻璃液温度最高,此处温度甚至可达1700℃以上。由于比重的差别,在电极附近就形成了玻璃液流,池深方向各层的玻璃都充分参加了这一流动,从而消除了高硼硅玻璃分层所带来的问题。另外,电极端部在玻璃液中的“放热”现象及由此而产生的玻璃液流提高了底层玻璃液的温度,加快了石英颗粒的溶解速度,促进了玻璃的澄清和均化。
3.全电熔玻璃窑炉
3.1.减少挥发的机理
全电熔厚料层垂直深层电熔工艺,熔化池表面复盖冷的配合料,配合料在复盖层下加热,从加热到玻璃形成的四个阶段,都在同一个地点,不同的时间和不同的垂直高度上完成。因此,它可以基本避免在火焰池窑中所造成硼挥发的存在条件。其机理是:
(a)配合料层表面工作状态平稳。全电熔厚料层熔制玻璃时,由于配合料是很好的绝热材料,料层的表面温度可低达200℃以下,而且料层表面没有任何火焰和高温高速气流的冲击,处于平稳状态,基本上可以避免“飞料”的物理损耗。
(b)冷炉顶可以回收挥发物。厚料层的料层厚度一般在100~200mm,表面温度在200℃以下。从一幅典型的熔制高硼硅玻璃的冷炉顶图1中,可以看到配合料表面0~40mm这一层,温度稳定在120℃,仅水份在蒸发,可称为冷配合料层。深度在40~80mm,温度从120℃提高到250℃,硼酸开始分解,称为热配合料层,深度在80~110mm的温度变化最剧烈,从250℃上升到1000℃,完成了硼硅酸盐的反应过程,称为硼硅酸盐反应带,也可称轻质层。再下一层则是含有大量气泡和带有未熔化好砂粒的熔融玻璃,称为玻璃的熔融过程,也可称半熔层。在这层下面就是玻璃的澄清和均化区域。硼硅酸盐配合料从表面的料层到轻质层,经过温度从120~1000℃的热过程,必然会发生硼酸和硼砂在脱水期中的硼挥发,挥发物由下向上逸出时,遇到冷的表面配合料层凝结起来,便产生硼的回凝现象,而在反应过程中所产生的CO2和NOx气体很容易穿过疏松的配合料层逸出。因此,硼的挥发物可以在这里被回收。应用这个原理,同样可以回收其它含有氟、铅和硒玻璃的挥发性物质。由此也很容易解释薄料层全电熔熔制工艺中硼的挥发率较高(10%左右)的原因。
(c)澄清和均化在垂直深层方向中进行。在垂直深层电熔窑中,在工作流的作用下,玻璃液从半熔层垂直向下运动,流向流液洞(见图1),而玻璃中的气泡依靠斯托克斯的原理由下向上运动,由液面排出,完成了澄清和均化过程。这个过程与水平式火焰池窑熔制有较大的区别,它好象在垂直管道中进行,没有与空气相接触的自由表面,因此不可能产生硼从玻璃结合态中挥发的问题。
从上述的熔化机理,可清楚地看到,由于硼的烧损减少到极小的程度,玻璃成份波动小、稳定,这是获得优质硼硅酸盐玻璃的重要工艺条件之一。
3.2.厚料层垂直深层电熔技术
如果厚料层操作不当,不但得不到高质量的玻璃,反而会在玻璃中产生结石和条纹,使玻璃质量变坏。要达到稳定作业,厚料层电熔的基本工艺技术,大致如下:
(a)严格控制料层厚度:厚料层全电熔窑,料层的厚度是一项十分重要的工艺参数,正常操作的料层厚度在100~200mm。太厚的料层使其深层造成更多的冷配合料,熔融玻璃液面温度降低,玻璃熔化不好。同时由于料层的绝热作用,深层的配合料温度升高,软化生料,形成一个半硬壳层,可能伸长到与四周池壁搭接,形成料拱。气泡聚集在料拱下排不出去,玻璃液面很快下降,造成脱空现象,严重时会发生玻璃液流空的事故。为了防止料拱现象和使玻璃中气泡能顺利排出,配合料不能完全复盖熔化池的表面。按Sorg公司在VSM的全电熔窑的经验,配合料复盖的面积占液面90%,留出10%面积的光面。熔制普通玻璃,光面留在六角形的六个角上。熔制乳白玻璃光面留在中心。对矩形的电熔窑,在池壁四周留出75~150mm的距离。如果料层太薄,配合料表面温度很快上升,料层的保温作用和硼的回凝现象消失、达不到厚料层熔制工艺的目的。另外,加料必须是均匀铺盖在玻璃液面上。如果局部地方形成料堆,最后将使料堆下沉,热的玻璃液包住冷的生料,在玻璃中容易产生结石、气泡等缺陷。
(b)保证正常条件下的电 热平衡:当改变熔窑出料量时,若电工参数没有及时调整,很快打破了原来工作状态的电 热平衡条件,而转入不稳定状态,窑内温度分布曲线和玻璃液的运动轨迹都会发生改变。若加大出料量而输入功率不变时,玻璃液面温度下降,热点下沉,在窑内出现“过冷”现象,迫使玻璃液面下降,料层变厚,大量的配合料下沉,生料来不及熔化。反之,出料量变小时,玻璃液面温度升高。热点上移,在窑内出现过热现象,使生料熔化速度加快,料层变薄,液面提高,引起耐火材料和电极加速侵蚀。因此当改变出料量时,输入功率与出料量要匹配好,应尽量保持熔制工艺条件的电 热平衡。
(c)建立合理的熔制温度曲线和稳定的玻璃液流:窑内玻璃液的温度差异是产生玻璃液对流的原因,在厚料层垂直深层电熔工艺中,如温度场不合理,表面层(半熔层)未熔化好的玻璃液常因少量垂直对流进入工作流使熔化好的玻璃液变坏。正常情况下,半熔层中玻璃液小的对流将未熔化好的原料托浮起来,固定半熔层和冷料层的位置。当半熔的玻璃进入最高温度区的加热区时,玻璃熔融过程就结束了,进入玻璃的澄清均化区域,在这个区域内不要产生强烈的垂直对流,使所有玻璃都经过了相同的热过程,熔制出均匀度高的玻璃。因此在最高温度带的温度分布曲线要平坦,不要发生大的温差。根据这一原理设计的电熔窑的温度分布曲线,有助于获得热均匀性好的玻璃。
(d)要有足够的玻璃液深度:全电熔窑熔化硼硅玻璃,熔化率要比火焰窑高2-3倍,这样高的熔化率,又要在垂直深层方向上完成玻璃的澄清和均化,必须有一个足够的深度,满足玻璃在窑内的停留时间,池深与熔窑的生产能力和熔化率等因素有关,一般液深在900mm以上。例如高硼硅玻璃6m2电熔窑中,池深1.38m,在15-20 m2的VSM电熔窑中,池深2.2m。
3.3.几种典型的全电熔玻璃窑炉
3.3.1熔制钠钙玻璃全电熔窑炉
主要使用在以下一些地方:
(1)地处风景区,烧化石燃料产生的烟气及玻璃熔制过程中产生的粉尘严重影响风景区的风景。环保局要求该厂停业整顿或采取了烟气除尘的地方。
(2)玻璃质量要求特别高的品种。
(3)电价特别低的地方。如一些小的水电站附近。
3.3.2 熔制铅玻璃的全电熔窑炉
(1)铅玻璃的熔制
采用火焰加热的池窑熔制铅玻璃,这种工艺的一个主要缺点在于熔制过程中氧化铅的挥发,其挥发量比在电熔窑中熔制时增加10%。多年来,铅晶质玻璃是在单坩埚窑、多坩埚窑或日池窑中熔制的。上世纪六十年代以来,使用了单元窑、马蹄焰池窑,玻璃产量、质量有了很大提高。用坩埚窑熔化玻璃时,很难消除粘土坩埚引起的耐火材料结石。日池窑因玻璃液面波动,冲刷耐火材料也引起比较严重的耐火材料结石和条纹。换热式连续熔化的池窑,其缺点是熔化过程中氧化铅的挥发量大,玻璃易分层还原;玻璃对耐火材料的侵蚀比较严重,容易引起条纹以及空气污染。这种池窑一般用天然气或城市煤气作燃料。如果用重油,会污染玻璃。
1959年以前建成了第一座电加热坩埚窑,采用SiC或MoSi2加热元件(前者水平安装,后者垂直安装)。其功率消耗是相当高的。后来曾用过电辅助加热的日池窑。然而,上述电熔方法并不能克服氧化铅的严重挥发、耐火材料对玻璃的污染比较严重以及环境污染等主要缺陷。
(2)铅晶质玻璃电熔窑的现状及发展前景
由于铅晶质玻璃易挥发、分层、还原等特性,因而在池窑熔化中对温度、气氛、窑压、对流等工艺参数非常敏感。通过实践及对各种燃料、窑型的综合分析,英国、瑞典、捷克及西德各国都一致认为全电熔窑是最为合理的,也是比较经济的。
近十几年来许多国家对于全电熔窑进行了研究,取得了重大突破。现在世界上已有不少电熔窑,它的优越性越来越为人们所注意。
前苏联及东欧国家大力发展电熔晶质玻璃技术。前苏联上世纪七十年代初进行工业性试验,七四年推广。在基辅、古雪夫、列宁格勒、乌克兰、明斯克等艺术玻璃厂采用,获得了良好的技术经济效益。
电熔窑在正常操作中,当熔化池玻璃液中的电极附近温度为1370℃时,熔化池上部空间仅120℃左右。这是因为在玻璃液的表面有几公分厚的配合料冷料层,消除了氧化铅的挥发(一般火焰熔化池窑中氧化铅的挥发高达10%),使窑内玻璃组成均匀稳定,同时使粉料成本降低、环境污染减少,总之,电熔窑耗电量虽然较大,却节约了大量氧化铅,因而电熔窑还是经济合算的。
(3)铅晶质玻璃全电熔窑内电极的选用
目前在铅玻璃全电熔窑上使用的电极有两种,一种是氧化锡电极,特点是抗还原能力差,适用于氧化性玻璃;另一种是钼电极,特点是抗氧化能力差,适用于还原性玻璃。氧化锡电极非常适用于熔制铅玻璃。在熔制铅玻璃的电熔窑中,如果使用钼电极,会在不同程度上受到氧化,并且玻璃中的氧化铅被还原,生成金属铅沉到熔化池底,这样设计的电熔窑必须每天在池底放料。
(4)我国铅玻璃电熔窑的现状及发展前景
我国铅玻璃电熔窑目前主要使用在以下几个地方:
- 铅晶质玻璃器皿。
- 光学玻璃。
- 宝石玻璃。
- 灯饰玻璃。后三者都必须与铂金坩埚共同使用。
(5)我国铅玻璃电熔窑使用的窑型
我国铅玻璃电熔窑使用的窑型主要有:
(a)T型窑:即上大下小的形状,氧化锡电极垂直安装在两边的台阶上,采用单相供电或三相SCOT供电。
(b)矩形窑: 上下大小的一样,氧化锡电极水平安装在两边的池壁上,采用单相供电或三相SCOT供电。
(6)我国铅玻璃电熔窑有待改进的地方
我国铅玻璃电熔窑使用中常出现一些问题有:
(a)水套与银杆断开,由于设计上或操作的不当,六支银杆全部断在氧化锡电极内,造成无法供电。
(b)氧化锡电极的头部断在窑炉内。
出现上述问题的原因的设计人员没有掌握铅玻璃电熔窑的一些特点。
3.3.3 熔制硼硅酸盐玻璃的全电熔窑炉
硼硅酸盐玻璃在传统的火焰池窑熔制过程中,常常会遇到硼的挥发逸散损失的问题。硼的挥发不仅使玻璃液不均匀,恶化玻璃质量,而且还白白地损失了价格昂贵的硼原料。因此,国外对减少硼的挥发问题进行了长期研究。迄今为止,硼的挥发率在10~15%,如果采用无水硼砂或硼酐作原料,可以降低到5~10%。
自从厚料层垂直深层全电熔窑出现后,给高硼硅玻璃的熔化带来了新方法,大幅度降低了硼的挥发。采用这种方法使硼的挥发率降低到1~2%。我国硼硅玻璃的生产基本上采用火焰窑。在高硼硅玻璃系统中,玻璃质量达不到理想程度。
(1)高硼硅玻璃熔化特点
高硼硅玻璃在科学实验和日常生活中有着广泛的用途,其制品有:各种烧器、量器、各种实验室用分析食品及各种玻璃化工管道。在科研教学单位的实验室、工矿企业及太阳能综合利用设备上都可以见到用高硼硅玻璃制做的各种产品。由于高硼硅玻璃产品用途的特殊性,决定了这种玻璃必须具备有良好的热稳性和化稳性。,目前国内外高硼硅玻璃的化学组成基本上如下表1所列。
表1 国内外高硼硅玻璃的化学成分及热膨胀系数α
牌号 Copyright © 江苏镇江陈金方玻璃电熔窑炉工程中心 版权所有 2010-2012 地址:镇江市学府路80号 电话:0511-88791451 手机:13951280541
|